1.2367 ESR bars
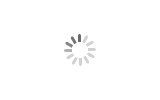
- pinxin
- huangshi
- within 45days
- 500 Ton/Tons per Month
DIN 1.2367 ESR is a chromium-molybdenum-vanadium alloyed hot work tool steel with high
thermal fatigue resistance. It has been refined via ESR process to ensure highest quality standards in terms of grain
size, segregation, micro-cleanliness, and purity. EN DIN 1.2367 features high isotropy, reason for which transversal
resilience is often three times higher when compared to conventional EN DIN 1.2367. Furthermore, the thermal
fatigue resistance is also often much higher than that of conventional hot work tool steel EN DIN 1.2343, enabling
longer die lifetime.
Applications
EN DIN 1.2367 ESR is used with great success in making inserts for light alloys die casting dies (for aluminium, Zamak, magnesium and brass), as well as for thermosets and thermoplastic injection molding dies. Further applications of EN DIN 1.2367 ESR are: light alloys extrusion tooling, such as liners, mandrels, pressure pads, extrusion stems and dies; forging and hot stamping of light and heavy metals; closed dies, punches, stamps and jaws; hot rolling rolls, as well as hot cutting applications, such as circular cutting blades, straight cutting blades and angular cutting blades.
Heat Treatment Like most tool steels, hot work tool steel grade EN DIN 1.2367 ESR obtains its optimized mechanical and physical properties through a corresponding heat treatment before final machining. The following provides a general heat treatment guideline.
Austenization Heating from room temperature to 650 °C (duration 2 hours). Hold for homogenization at 650 °C for 2 hours. Heating to 850 °C (duration 2 hours). Hold for homogenization at 850 °C for 2 hours. Heating to temperature of austenization: 1030-1080 °C. Hold at austenization temperature for 45 minutes. Cool down in oil, salt bath at 500 °C, or air. At any case, the decarburized layer should be removed. Oil bath cooling should be stopped, when the temperature reaches 200 °C, thereafter cool in air until reaching 50-80 °C.