4140 Case Hardening Structure Steel
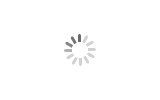
- pinxin
- huangshi
- within 30-45days
- 5000 Ton/Tons per Year
4140 alloy structural steel. This steel has good workability and small processing deformation. The fatigue resistance of 4140 alloy structural steel is quite good. It is a medium-sized hardenable steel. 4140 has good strength and good comprehensive mechanical properties after heat treatment. Good manufacturability and high yield. The highest operating temperature is 427 degrees Celsius. 4140 strength, high hardenability, good toughness, small deformation during quenching, high creep strength and enduring strength at high temperatures.
Comparable Standards:
AISI/SAE | DIN | W.Nr. | AFNOR | JIS | BS | SIAU | GB,YB |
4140 | 42CrMo4 | 1.7225 | 42CD4 | SCM440 | 708A42 | UM8 | 42CrM. |
4140 Chemical Analysis (%):
C | Mn | Si | Cr | Ni | Mo | P | S |
0.38-0.45 | 0.50-0.80 | 0.17-0.37 | 0.9-1.20 | max 0.030 | 0.15-0.25 | max 0.035 | max0.035 |
4140 steel is ultra-high-strength steel with high strength and toughness, good hardenability, no obvious temper brittleness, high fatigue limit and multiple impact resistance after quenching and tempering, and good low-temperature impact toughness. 4140 steel is suitable for manufacturing large and medium-sized plastic molds that require certain strength and toughness.
Mechanical properties
Hardness: Annealed, 147~241HB, 42CrMo
4140 mechanical properties:
Tensile strength σb (MPa): ≥1080(110)
Yield strength σs (MPa): ≥930(95)
Elongation δ5 (%): ≥12
Reduction of area ψ (%): ≥45
Impact energy Akv (J): ≥63
Impact toughness value αkv (J/cm2): ≥78(8)
Hardness: ≤217HB
In order to increase the mold life to more than 800,000 mold times, the hardening method of quenching and low temperature tempering can be implemented on the pre-hardened steel. When quenching, preheat it at 500-600℃ for 2-4 hours, then keep it at 850-880℃ for a certain period of time (at least 2 hours), put it in oil and cool to 50-100℃ and air cooling, the hardness can reach 50 after quenching -52HRC, in order to prevent cracking, 200℃ low temperature tempering treatment should be carried out immediately. After tempering, the hardness can be maintained above 48HRC.
Corresponding grade
Russia ГOCT 38XM, the United States AISI 4140/4142, the United Kingdom BS 708M40/708A42/709M40, France NF 40CD4/42CD4, Germany DIN 41CrMo4/42CrMo4, Japan JIS SCM4, international ISO 683/1 3
Quenching specification
Common quenching and tempering specifications: quenching temperature 1000~1050℃, quenching oil or quenching gas, hardness ≥ 60HRC; tempering temperature 160~180℃, tempering time 2h, or tempering temperature 325~375℃, number of tempering 2 ~3 times.
Process specification
Hot working specification
The heating temperature is 1150 ~1200°C, the starting temperature is 1130 ~1180°C, and the ending temperature is> 850°C, when φ> 50mm, slow cooling.
Normalizing norms
The normalizing temperature is 850~900°C, and the furnace is air-cooled.
High temperature tempering specification
The tempering temperature is 680~700°C, and the furnace is air-cooled.
Quenching and tempering specifications
Preheating temperature is 680~700°C, quenching temperature is 840~880°C, oil cooling, tempering temperature is 580°C, water cooling or oil cooling, hardness ≤217HBW.
Specification for sub-temperature quenching strengthening and toughening treatment
Quenching temperature 900°C, tempering temperature 560°C, hardness (37±1) HRC
Specification for induction hardening and tempering
The quenching temperature is 900°C, the tempering temperature is 150~180°C, and the hardness is 54~60HRC.